Why Choose Ecoat?
Information taken from our paint supplier PPG Ecoat
Why Choose Ecoat?
The choice of electrocoat over other coating technologies is usually driven by the lower total applied cost of electrocoat. The low total applied cost is made possible because electrocoating is an automated, precise film build, high paint transfer efficiency process. The process yields a consistent part-to-part, high performing coating, with no need to inspect or re-work parts due to paint defects such as runs, sags and voids.
The key to electrocoat’s high paint transfer efficiency can be summarized in two parts:
⦁ The process automatically limits the amount of paint being applied. As paint film builds on the surface, an insulating layer is built which resists the deposition of excess paint.
⦁ By using ultrafiltration, the process can recover over 98% of all paint that is carried out of the paint tank and into the rinse stages.
The process also provides the end user the ability to coat complex parts or hard to reach surfaces, while still hanging parts very densely. Combined with the fact that manual labor is not needed to apply paint, the electrocoat system becomes a fast moving and highly productive coating process.
Environmental advantages include products with low or zero VOC and HAPs, often eliminating the need for costly air abatement equipment that is present with many solvent based liquid spray or dip processes. Electrocoat products are heavy metal-free and have low BOD/COD if introduced to waste streams. Products are water-based, thus reducing fire hazards and worker exposure to hazardous materials.
Advantages of selecting electrocoating technology
Application & Performance
⦁ Outstanding Film Uniformity: Consistent film on all part-to-part surfaces. No sags, runs, or drips.
⦁ Total Coverage of Complex Part Configurations: Coating on all recessed areas and sharp edges.
⦁ Precise Film Build Control: Use DC voltage to deposit paint only where it is needed.
⦁ Pre-Assembly Before Coating: Less post paint rejects.
⦁ Wide Range of Products: Formulated to meet corrosion, durability and other performance specifications.
⦁ Flexibility: Multiple part configurations can be coated in one tank, without having to change the application equipment.
Economics
⦁ Totally Automated Process: No direct labor.
⦁ Very High Productivity: Dense and non-uniform line loading.
⦁ Very High Transfer Efficiency: Closed-loop rinse system approaches 100%.
⦁ Lower Energy Requirements: No dry-off oven; minimal exhaust and air make-up.
⦁ Minimal Maintenance: Minimal hook cleaning; no “booth” maintenance.
⦁ Lower Insurance Rates: No specific fire or health hazards.
Environmental
⦁ Minimal Solid Waste: Closed-loop rinse system reduces paint loss.
⦁ Reduced Fire Hazard: Waterborne systems.
⦁ EPA Compliance: Low or zero VOC and HAPs coatings.
⦁ OSHA Compliance: No special personal protection.
⦁ Cleaner Application: Totally enclosed system.
⦁ Recycled Water: Closed loop system reduces water loss.
Pretreatment Process for Electrocoat Paint Application
In the pretreatment process, metal surfaces are cleaned and prepared for electrocoat paint application. Oils and other contaminants are removed from the part. Existing rust spots may be removed and a phosphate or conversion coating is applied. The pretreatment process is necessary to improve electrocoat performance, ensure a high quality electrocoat finish and to keep the paint bath clean of unwanted contaminants. The number and type of pretreatment stages depends greatly on the type and condition of metal being introduced to the system. It also depends on the part configuration and the overall performance requirements of the phosphate or conversion coating.
Zinc and iron phosphates are the most widely used conversion coatings in the electrocoat industry. Zinc phosphate is the preferred pretreatment choice in the electrocoat industry because it provides the best corrosion resistance and paint adhesion. Iron phosphating has had a long history of being the process of choice for applications where overall cost considerations override performance requirements. Although iron phosphates provide reduced corrosion resistance in comparison to a zinc phosphate process, it is less expensive to install and operate.
Non-phosphated, zirconium-based conversion coatings are becoming more common in the finishing industry. For several years, they have been replacing iron phosphates because of their low operating costs, multi-metal applications and environmental friendliness. When used in electrocoat applications, their performance usually falls short of a zinc-phosphate process. However, because of their installation and operating cost savings, zirconium processes are now being considered and evaluated where only zinc phosphate is currently approved.
Electrocoat Bath Process
The electrocoat bath consists of deionized water and paint solids. The deionized water acts as the carrier for the paint solids, which is under constant agitation. The paint solids consist of resin and pigment. Resin is the backbone of the final paint film and provides corrosion protection, durability, and toughness. Pigments are used to provide color and gloss.
The electrocoat process is driven by a DC rectifier, used to regulate and control the paint film build on the parts. The tank contains electrodes, which carry an electric charge that is the same as the paint particles and opposite of the metal parts being coated. When voltage is applied from the rectifier, paint is driven away from the electrodes and to the part where it is electrodeposited to the metal surface. Often, the electrodes are surrounded with semi-permeable membranes that are used to control bath pH. The paint tank uses pumps to provide the agitation necessary to feed particle filters which keep the paint clean. The pumps also feed the ultrafilters, which generate post rinse permeate and feed heat exchangers so that the paint bath temperature can be controlled. The tank and all of the supporting equipment are custom designed and sized to meet the coated surface area per minute demand.
Post Rinse Process for Electrocoated Parts
As the painted part exits the electrocoat bath, undeposited paint clings to its surface. This undeposited paint is commonly referred to as drag-out or cream coat, and multiple rinse stages are usually incorporated into the system design for its removal and improvement of the final aesthetic appearance of the part. Whereas the cream coat will be rinsed away, the electrodeposited paint has bonded with the surface and will remain intact during the post rinsing process.
Post rinsing stages are in a closed loop with the paint tank, as they are continuously being fed with fresh ultrafilter permeate from the paint tank. As they fill up, they either gravity or mechanically overflow to the prior rinse stage and eventually the paint tank. The end result is a painting process that has an application transfer efficiency of over 98%, as almost all of the drag out or cream coat is captured in the post rinses and returned to the paint tank.
Some systems also make use of a final post rinse stage that is made of deionized water. Although not part of the closed loop rinsing process where cream coat solids are recovered, and not required when the electrocoat will be top coated, a final deionized water rinse will help to improve the appearance of an electrocoat finish.
Why Choose Ecoat? (ppgecoat.com)
Bake Oven Process for Electrocoated Parts
After exiting the post rinses the electrocoated part enters the bake oven. The bake oven crosslinks and cures the paint film, making it hard and durable to assure maximum performance properties. Oven temperatures can range from 180°F to over 400°F, largely dependent on the paint technology being used and the time spent in the oven. Most often, 20 minutes of metal temperature at a recommended temperature is specified to obtain full paint cure.
Because of their water based formulations, electrocoat paints have low volatile organic compound (VOC) and hazardous air pollutant (HAP) content. Ovens must be continuously exhausted to maintain the oven atmosphere below the lower explosion limit (LEL) and to prevent smoke buildup in the oven and plant. Often, the levels of VOC or HAP emissions are low enough that companies are typically permitted to exhaust ovens to the atmosphere without the use of air abatement equipment. Federal, state and local law will define the amount of emissions that are permitted without the use of air abatement equipment such as a thermal incinerator.
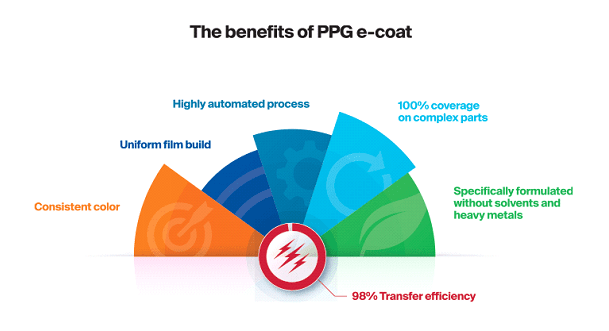