Electrophoretic Painting
What is Electrodeposition?
Electrodeposition is a method of applying paint to a conductive substrate where paint particles, suspended in water, are given an electrical charge allowing them to deposit on substrates of the opposite charge when influenced by a direct current.
The resultant paint finish is of a high aesthetic standard affording strong durability and resistance to corrosion and the effects of corrosive liquids and chemicals.
Over the years the process has been modified to remove all hazardous air together with virtually all volatile polluting solvents organic compounds. Equally, the process used by Profin contains no lead compounds or chromium in any format.
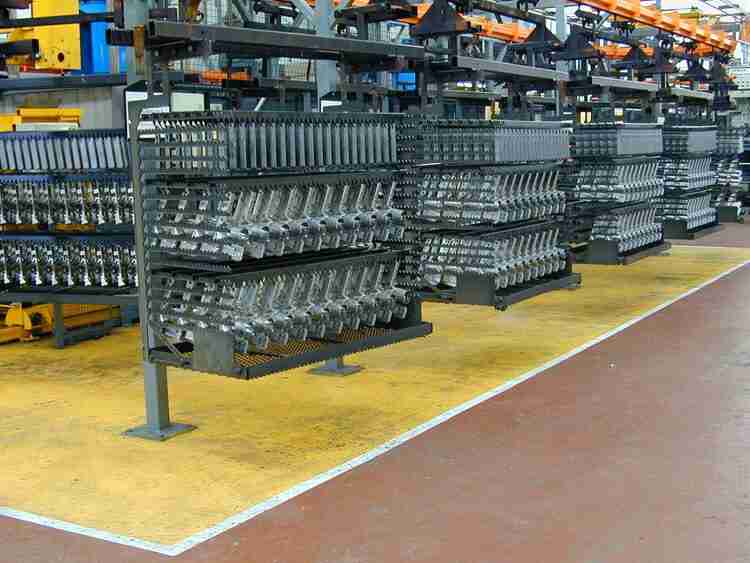
Electrophoretic Painting
The success of the electrophoretic painting process is dependent upon the integrity of the pre-treatment processes as well as the painting process itself. In order to present the components in a fit state for painting, they must first undertake a series of preliminary processes which are outlined in more detail on the subsequent pages.
Briefly the preliminary processes are as follows: –
- Cleaning to remove all debris and lubricants from the components.
- Rinsing to remove any excess cleaner.
- Conditioning to chemically prepare the surface of the components for subsequent treatment
- Phosphating in order to change the surface and formulate a phosphate film on the surface which has the ideal grain configuration for painting.
- Rinsing to remove excess phosphate.
- Sealing in order to seal the process prior to painting.
- Rinsing to remove excess phosphate.
- Sealing in order to seal the process prior to painting.
- Rinsing to remove excess sealer.
- The electrophoretic painting operation itself.
- Rinsing to remove excess paint using ultra filtrated water.
- Final rinse using de-ionised water
- Stoving through a gas fired oven.
Cleaning
In order to remove all debris, oils and contaminants, a series of different cleaners used in the first three process tanks. These vary from a low strength ‘knock-off’ cleaner to a highly caustic powder cleaner. All three cleaners are effective on a wide variety of oils and greases. The high alkalinity helps shift some types of soil although the level of caustic is not sufficient to de-rust effectively.
The two current drawbacks are, firstly, the high temperature needed to guarantee good performance and, secondly, the fast ‘dry off’ between process steps. This can cause a build-up of rinse residues that show up on the part as ‘mapping’.
Occasionally oils and greases are encountered which cannot be removed by the three cleaners used. When this situation arises, the parts are degreased using either our cleaning plant or the iron phosphate and cleaning plant.
Rinsing
It is absolutely imperative that any excess cleaning solution is removed prior to further processing. Consequently, following on from the cleaning tanks are two rinses tanks. These tanks are filled with cold town’s water agitated by passing air through the water. The fifth tank has a steady flow of water feeding into the tank which subsequently feeds into the fourth tank. By using this method the fifth tank is kept clean and free from contamination
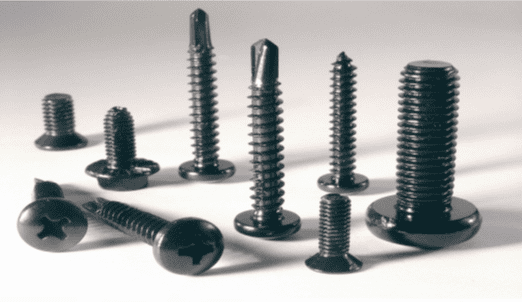
Conditioning
The sixth tank in the process contains a conditioning rinse for the phosphating process. The solution contains Titanium that helps prepare the metal to refine the correct size and shape of the phosphate crystals. It has been proven that powder conditioners are more effective than the liquid types.
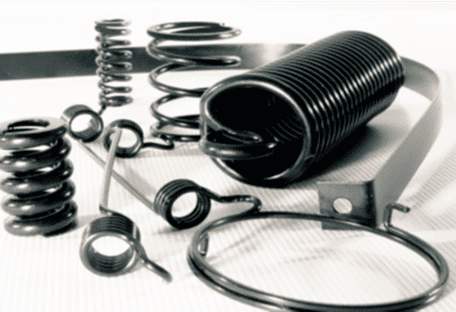
Special points of interest
- Salt spray resistance to a 1,000 hour as per ISO 7253
- Cyclic testing to 60 cycles in accordance with DIN 53167
- Cyclic testing to 10 cycles in accordance with VDA 621.415
- Cyclic testing to 150 cycles in accordance with Nissan CCT1
- Humidity resistance in accordance with DIN 50017
- Adhesion in accordance with ISO2409 to GtO
- Persoz hardness in accordance with ISO1522 greater than 300
- Pencil hardness in accordance with ASTM D3363-92A at 4H+
- Direct impact in accordance with NFT 30-017 to 1Kg/ 1m.
Zinc Phosphating
It is absolutely imperative that any excess zinc phosphate solution is removed prior to further processing.
Consequently, following on from the zinc phosphate tanks are two rinse tanks similar to those following on from the cleaning tanks. Again, these tanks are filled with cold town’s water agitated by passing air through the water. The ninth tank has a steady flow of water feeding into the tank which subsequently feeds into the eighth tank. By using this method, the ninth tank is kept clean and free from contamination.
Sealing
The solution contained in the eleventh tank is a chromium-free, inorganic-based post rinse, formulated for use after the zinc phosphating pre-treatment process and prior to painting, or powder coating. Its use will materially improve the overall system performance. This solution can either be used as a spray or immersion system.
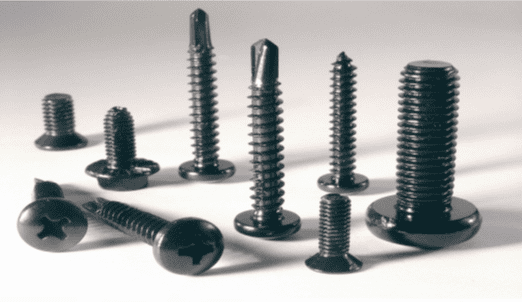
Electrophoretic Painting
Electrophoretic painting was originally conceived in 1961. The original system used an ‘anionic’ system where the part is positive and the paint is negative. This gives rise to an economical coating system where the curing time is relatively low and the corrosion resistance is reasonably high. In 1971 the first ‘cationic’ system was evolved. This new system had many advantages over the anionic system, particularly with reference to the automotive industry requirements. These advantages include:
- Improved corrosion resistance at low film builds.
- Increased ‘throw power’ in recessed areas with no increase in overall film build.
- Improvements in bimetallic corrosion allowing for a wider use of construction materials in product design.
- Better adhesion over galvanised substrates
- Improved electrical efficiency along with higher operating temperatures reducing energy costs.
Following painting, the components are rinsed through two tanks of ultra-filtrate water (UF), in order to remove any excess paint, followed by one tank of de-ionised water (DI), to remove any last vestiges 0f paint, foreign objects, etc. prior to stoving. The carriers are then returned to the conveyor to be transported to the oven where they are then stoved, or cured, through the oven at 185 degrees Centigrade for approximately one hour.